はじめまして。重工メーカーで機械設計をしているベルといいます!
このページでは「機械設計のセンスの磨き方」を自身の体験をもとに一つ解説します
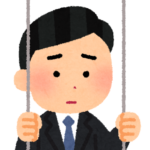
- 機械設計のセンスが自分にはない…
- 機械設計の力に伸び悩みを感じる…
以上のような、機械設計のセンスや伸び悩みを感じる方への解決方法をご紹介します
この記事の内容
- 機械設計のセンスを磨く方法
- 機械設計の能力の伸び悩みを解消する方法
- 解決方法の取り組み方
私自身、重工メーカーに就職して5年以上、機械設計だけしてきました
ここ最近同じことばかりしているように感じ、成長している実感がありませんでした。
それにも関わらず、設計ミスや後戻りを発生させることもあり、機械設計のセンスがないことにも悩んでいました。
そんな時に、”あること”をしてから、急に視界が広がったような体験をし、悩みを解決することができたのです。
この経験に基づいて記事を書いていますので、もし同じ境遇の方や、同じ悩みを持っている方に読んでいただければ参考になるかと思います
この記事の解決方法を試してみていただき、皆さんの機械設計のセンスに磨きをかけるきっかけになれば幸いです
機械設計のセンスの磨き方は=機械の整備・点検を自分で行うこと
機械設計のセンスの磨き方は、「自分の設計している機械の整備・点検を自分で行うこと」です
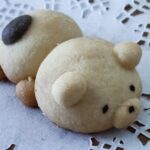
ここでいう”機械設計のセンス”は「設計する時に部品の取り付けやすさや、メンテナンス性、操作性まで考えて図面に反映できる能力」とします
なぜなら、自身が設計した部品一つ一つを図面と実物を真剣に比較することになるためです。
例えば、機械を分解するときには次のようなことを考える必要があります。
- 分解するにはどの順番ではずせばよいか?
- 取り出した部品はまだ使えるのか?
- この部品はなぜこのような消耗の仕方をしているのか?
- 取り外した部品には一時的に何かを塗布しておく必要があるのか?
- この部品は手入れしたら再使用できるのか?
使用済みの機械を分解する時は、とにかく新品の機械を組み立てるのとは考え方が全く違います。
このような疑問や考えを、自分の机よりも不便な現場で、しかも時間に追われながら考え抜いて結論を出す必要があります
かなりのストレスを感じますが、その分この時の経験がかなり強烈に脳に焼き付きます
したがって、機械設計のセンスを飛躍的に伸ばしたい方は整備・点検を自身の手で体験することをおすすめします。
重工製品のような巨大な機械の整備・点検では、実際に手を動かすのは下請業者になることが多いとは思いますが、整備・点検の担当者として赴いている場合、自分自身がほぼすべての部品の分解・整備を見て、必要であれば触れてみて対応する必要があります。
そのため、ほとんどの作業で自分が手を動かさなくても、自身が強烈な体感する場面は必ずやってきます。
整備・点検をするとどういった点で磨きがかかる?
- 部品の分解・組立のしやすい構造にするセンス
- コストダウンできるところを見抜くセンス
- わかりやすい組立図を作るセンス
以上3点について特にセンスに磨きがかかります。
なぜなら、自らが分解・組立を行うため、
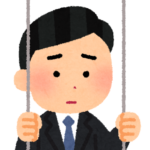
- ここの形状がもっとこうなっていたらな
- この部品、はずしにくいな
- この組立図わかりにくい!
といったことを身を持って知ることになるためです。
例えば、回して分解する部品があるとします。
部品としては、加工も簡単で機能も満たすことができるただの円形状でも問題ありません。
一方「メンテナンスがしやすいか?」という視点ではどうでしょうか?
きれいな円形状のままでは、人の手ではつかみどころがなく、取り外しにくい形状になります。
この場合、少し加工して凹ませるだけでも、回しやすくすることができます。
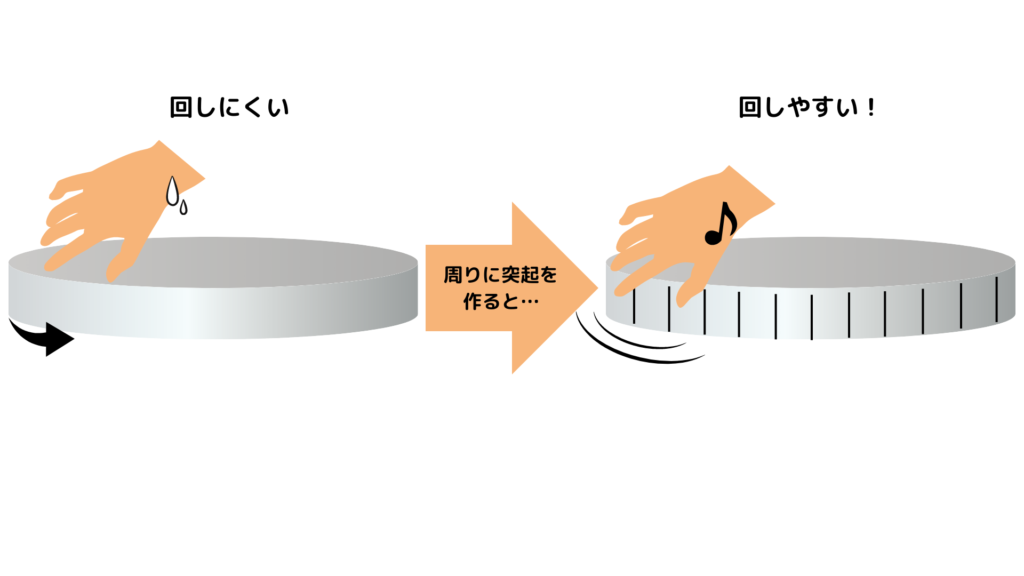
設計段階では、このようなメンテナンス性の視点が抜けがちです。
実際に触ってみないと気づきにくいということも要因の一つでしょう。
そこで、整備・点検で実際に手を触れることにより、
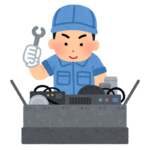
- ここもっと動かしやすくしたいな
- この姿勢でしか取り出せない部品はできるだけ軽くしたいな
といったことを身を持って体験することになります。
その結果、設計時に組付け方法を想像する際に「このままでは取り外ししにくいのでは?」と、メンテナンス性を改善するセンスを獲得することができるようになります。
また機械を分解していると、「この部品、全然消耗していないな」と感じる部品がいくつか出てきます。
この場合、メンテナンス期間を考慮したらオーバースペックになってしまっていることが考えられるため、
- より安価な材料に変更する
- 部品を小さく、薄くする
ことでコストダウンできそうな部品を見つけ出すことができます。
また似ている構造の場所があれば、同じような部品が、同じような消耗具合になる可能性が高いため、作図時点からコストダウンできる箇所を見抜く力も鍛えられます。
さらに、機械の整備・分解は組立図面をまじまじと見ながら行うことになります。
この時によく感じることが、
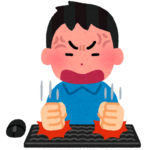
- 図面にほしい情報が載ってねぇ!
- 部品同士の関係がわからねぇ!
という、作図者を呪いたくなるような組立図面になっていることがあります。
(※作図者が自分の場合あり)
この時に感じた組立図に対する不満が、そのまま組立図をセンス良く作る力につながるのです。
不満点を解消できるように組立図に落とし込むことで、
- 点検時に図面1枚でスムーズに作業できるようになる
- 誰でもどのように組立・分解すればいいのかわかる
といった点で改善できるようになり、他の組立図面を作るときにも「こういう情報があった方がいいな」というポイントがわかるようになるため、組立図面を作るセンスにも磨きがかかります。
したがって、整備・点検を自分で行うと、
- 部品の分解・組立をよりしやすく、
- コストダウンできるところを見抜き、
- わかりやすい組立図面を作る力
に磨きがかかります。
設計者でありながらどのようにして整備・点検の仕事に関わればよいか?
では設計部である人間がどのようにして整備。点検の仕事をすればよいのでしょうか?
純粋に「自分の力を伸ばしたいからやりたい」と上司に伝えるのが無難です。
私が実際に目にした方法としては次の二つがありました。
- 異動願いを出す
- 「勉強のために一度その仕事をやらせてほしい」と上司に相談する
あくまでも設計部には残っていたいのであれば、「勉強のために一度その仕事をさせてほしい」と伝える方法をおすすめします。
異動しなければその仕事をさせてもらえないのであれば、異動願いを申しでるしかないでしょう。
異動後も設計に居続けたいのであれば、期限付きの異動であることをきちんと伝えておくようにすべきですが、伝えたとしても、約束が守られる可能性はほぼないと思っていた方が無難です。
なぜなら、終わりの見えにくい仕事をやらされたり、あなたが有能であれば設計部になかなか戻してくれなくなったりするためです。
ちなみに私は後者の方法で整備・点検の仕事をさせてもらいました。
まとめ
機械の整備・点検をすることで、
- 部品の分解・組立のしやすい構造に変える
- コストダウンできるところを見抜く力
- わかりやすい組立図を作る製図能力
といった機械設計で重要なセンスを磨くことができます。
自らの目で、自らの手で一つ一つの部品に対応し、さらに現場のスピード感、緊張感の中で体験することは強烈に印象に残るため、一度行くだけでもかなり得るものが多くあります。
私自身も一度現場に行っただけでも、かなり多くのことを学ぶことができました。
したがって、
- 現在設計の仕事をしてマンネリ化している方
- 自身の設計の力に伸び悩みを感じている方
には特におすすめしたい方法です。
【コラム】重工製品の整備・点検について
重工製品の整備・点検ははっきり言ってめちゃくちゃきついです。
この記事を書いた裏の理由は、このことを伝えたいが為に書きました。
重工製品の整備・点検がきつい理由としては、主に次の通りです。
- 部品一つ一つが巨大で取り回しが大変
- 人が持てるぎりぎりの重量の部品が多い
- 重工製品の使用される環境は人体に有害な物質のものがある場合がある
- 重工製品は一般ユーザー向けに作られているわけではないため、メンテナンス性が悪い
例えば、重工製品が納められる場所としては主に発電所、製鉄所、化学プラントといった、人が接触したら即アウトになるような要素が数多く存在している環境になります。
そんな環境に生身で整備・点検を行うので、一歩間違えれば本当に命を落としかねません。
またそういった危険性があることに加え、重工製品は巨大が故、それを動かす動力源も強大なパワーを持っています。
整備・点検のために停止しており、万が一にも動かないようにもしていますが、整備や分解のため少しだけ動かしたりする必要が出てきてしまいます
その時に、誰かが手を入れていたり、身体を入れた状態であれば、人体にはとても耐えられない力がかかり…
したがって、もしこの記事を読んでくださり、さらに勉強のため整備の仕事をしようと考えてくださった場合には、どうか安全に配慮して整備・点検するようにしてください
分解時には、
- 「こんな場所の部品取り出せるわけない!」
- 「こんなものどうやって取り出すんだ!」
となる場面が多々あります
時には人が生身で、身体に無理をさせないと分解できないような場面も少なくないです
これがかなりきつい
いわゆる3K(きつい・汚い・危険)な職場に自分から赴くことになるため、本当に消耗します
点検・整備の仕事にこれから取り掛かろうとまでなってくださった場合は、それなりの覚悟を決めておいてください
ここまで読んでくださり、ありがとうございました